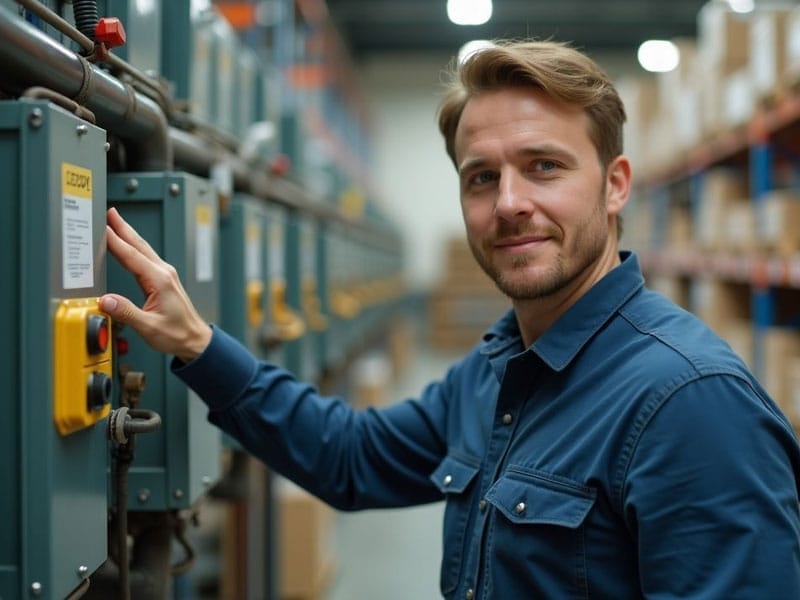
The Ultimate Indiana Contractor’s Guide to Electrical Components
Are you struggling with finding reliable electrical components for your industrial projects?
High-quality parts are essential to ensure safety and long-term performance in tough applications.
This guide will walk you through the key components Indiana electrical contractors need, from circuit breakers to wiring solutions.
Key Takeaways
- High-quality electrical components ensure safety, reliability, and efficiency in industrial projects. Poor-quality parts can cause risks, such as downtime or hazards.
- Circuit breakers vary by use, from MCCBs for heavy loads to GFCIs for water-prone areas. Proper selection boosts performance and safety.
- Reliable wiring solutions like shielded cables prevent interference, while armored cables offer extra protection for harsh conditions.
- Preventive maintenance, such as inspecting connections and testing breakers, avoids costly failures and extends system life.
- Safety devices like surge protectors and emergency disconnects reduce the risks of voltage spikes and accidents during operations.
The Critical Role of Quality Components in Industrial Applications
Well-made circuit breakers, power supplies, and wiring protect both systems and workers.
Reliable components like the National Electrical Code (NEC) meet strict industry standards.
High-quality items last longer and need less maintenance.
Choosing trusted suppliers with extensive inventory ensures durable parts at competitive prices for every job in Indiana.
Safety and reliability considerations

Using reliable electrical supplies ensures the safety of your projects.
Circuit breakers, switches, and panelboards must meet industry standards to prevent accidents like arc flashes or overloads.
Poor-quality components can fail under stress, putting workers at risk.
Always choose products designed for heavy-duty use in industrial settings to maintain reliability.
Emergency electrical services often rely on surge protection solutions and proper grounding practices.
“Safety starts with smart planning” applies well when selecting strain relief devices or wire connectors that handle high loads without issues.
Secure installations reduce downtime while enhancing energy efficiency over time.
Power Distribution Components
Choose top-quality electrical supplies for power distribution to ensure safe and efficient operations.
Types of circuit breakers and their applications
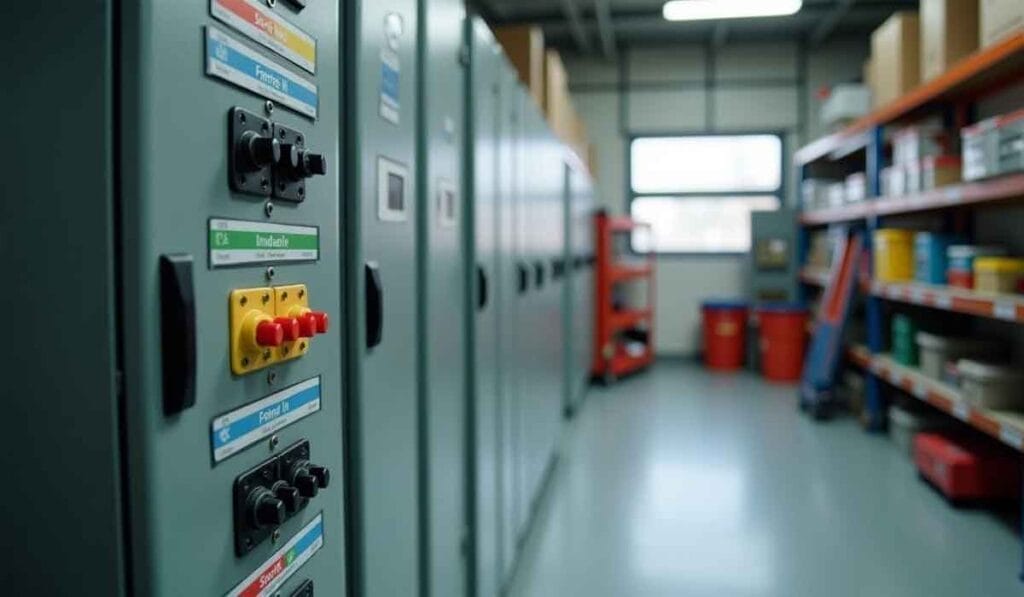
Circuit breakers are vital for electrical projects. They protect systems, prevent damage, and ensure safety.
- Molded Case Circuit Breakers (MCCBs)
These suit industrial applications. Use them in power distribution and motor protection for high current loads. - Miniature Circuit Breakers (MCBs)
These work well for low-current systems. Install them in residential or light-duty commercial setups. - Residual Current Circuit Breakers (RCCBs)
These detect ground faults and prevent shock hazards. They are best used in areas with high moisture levels, such as kitchens or bathrooms. - Air Circuit Breakers (ACBs)
These handle high voltages over 1,000 volts, making them ideal for heavy machinery or switchgear systems. - Vacuum Circuit Breakers (VCBs)
These operate efficiently in medium-voltage setups, such as factories or substations. - Oil Circuit Breakers
Use these in outdoor installations like transformers to control large voltage fluctuations. - Hybrid Switchgear-Circuit Breakers
These merge gas-insulated designs with vacuum components, ensuring compactness and reliability for modern setups. - Magnetic Circuit Breakers
Built to handle brief surges, they protect equipment like DC motors or CNC machines. - Thermal Magnetic Circuit Breakers
Apply these in environments needing dual protection against overloads and short circuits. - Ground Fault Circuit Interrupters (GFCIs)
You can install these to prevent electric shocks near water fixtures such as pool areas or basements.
Transformer selection and specifications
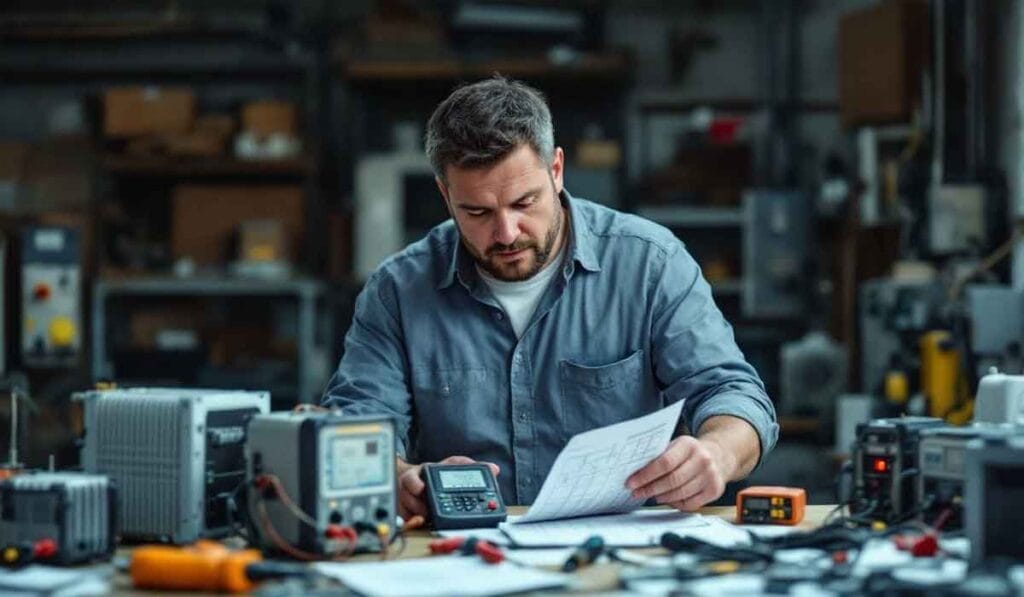
Choosing the right transformer for your electrical projects is crucial. It ensures safety, efficiency, and proper functioning.
- Select a transformer based on power needs. Check the voltage and wattage requirements of your project.
- Choose between step-up or step-down transformers. Step-up increases voltage, while step-down reduces it.
- Ensure compatibility with industrial and commercial standards like ANSI or UL certifications.
- Factor in operating temperature. Transformers with thermal management systems can handle heat better.
- Use oil coolers for high-load applications to avoid overheating.
- Consider energy-efficient models for lower running costs and reduced energy consumption.
- Match the right size to your project demands to avoid overloading or wasting capacity.
- Verify that the insulation type withstands environmental conditions such as moisture or dust.
- Check frequency ratings (50Hz or 60Hz) to match the grid supply in your area.
- Look for built-in surge protection features to guard against voltage spikes during operation.
- Use transformers suitable for harsh environments in industries like aerospace or automotive manufacturing.
- Opt for units with easy maintenance access to reduce downtime and repair costs if issues occur during use.
Selecting correctly avoids future problems and ensures safety during electrical installations in your projects.
Power distribution systems
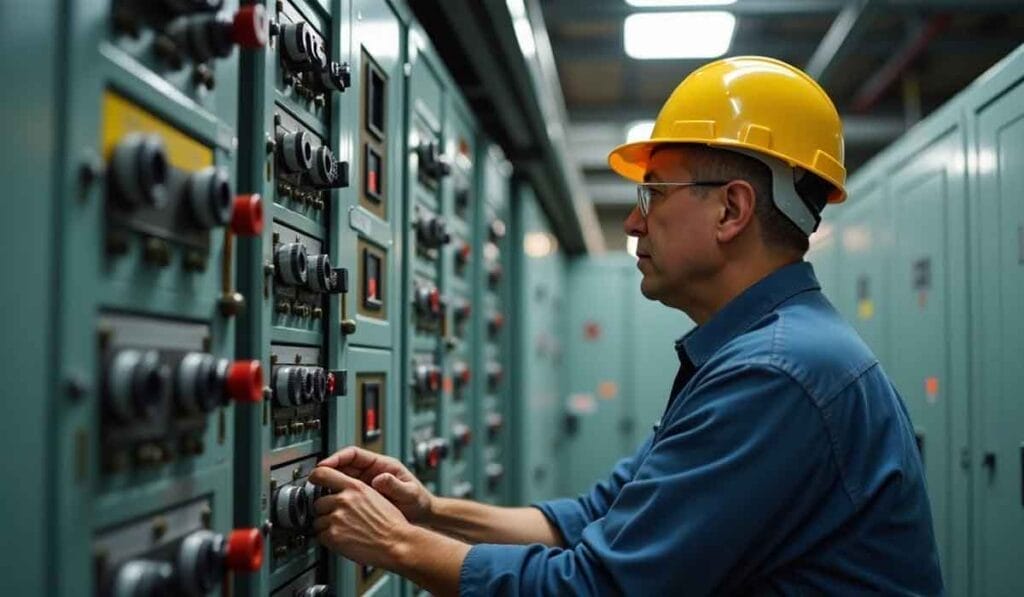
Transformers deliver power efficiently, but power systems distribute it where needed.
Switchgear ensures control and safety in these setups, and circuit breakers protect against overloads and arc flash hazards.
Proper distribution prevents costly downtime in electrical projects. Industrial-grade components improve energy savings and system reliability.
Reliable wiring is crucial for steady power flow in factories or construction sites. Electrical conduits shield cables from damage while keeping installations clean.
Well-designed switchgear panels optimize performance for heavy-duty tasks like milling or operating programmable logic controllers (PLCs).
Quality equipment ensures safe connections during demanding jobs in aerospace or automotive production.
Safety and Protection Devices
Safety devices can prevent equipment failure and workplace accidents. Use them to protect people, tools, and electrical systems.
Circuit protection mechanisms
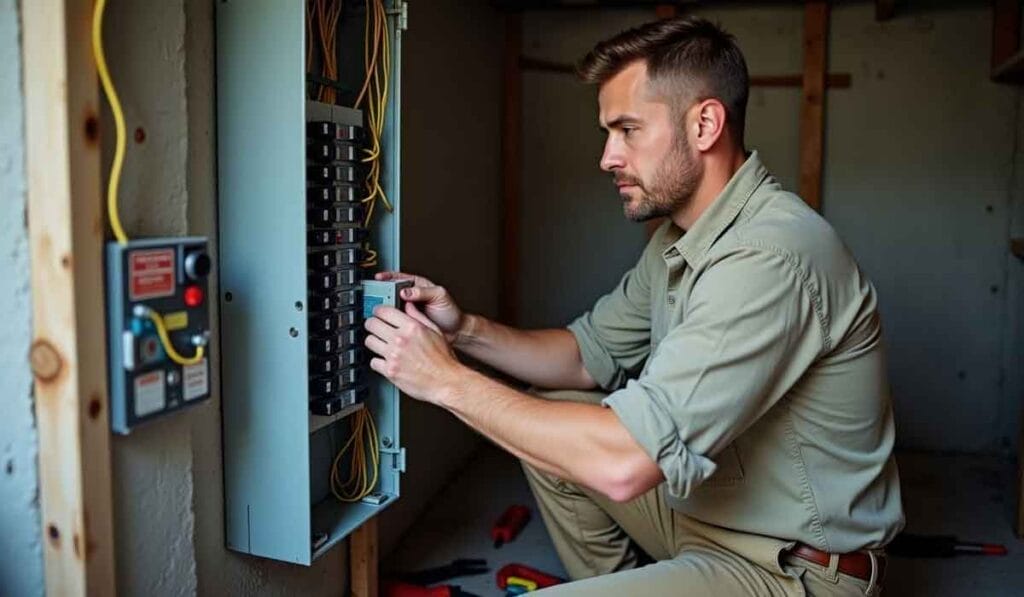
Circuit protection mechanisms keep your electrical projects safe and efficient.
They protect systems from overload, short circuits, and other risks.
- Install circuit breakers to prevent system overloads. These devices stop electricity when the current exceeds a set limit. Choose the right type based on your electrical wire capacity.
- Use fuses to guard against excessive current flows. Once blown, replace them to restore power safely.
- Ground fault circuit interrupters (GFCIs) should be applied near water sources. These prevent shock by stopping the current in case of faults.
- Add arc flash protection for industrial applications with heavy equipment like CNC machining tools or electric drills.
- Surge protectors shield sensitive electronics from sudden voltage spikes. They are essential for printed circuit boards and programmable logic controllers (PLCs).
- Emergency disconnects provide a quick way to cut power during hazards. Contractors must prioritize this feature in emergency electrical services setups.
- Thermal relays protect motors from overheating. They ensure equipment like band saws runs within its temperature limits.
- Utilize overcurrent relays for larger power distribution systems such as transformers or gray iron plants.
- Apply proper insulation and wiring techniques to avoid tripping protective devices unnecessarily.
- Follow safety standards when handling these mechanisms to comply with regulations and ensure reliable performance across all systems.
Surge protection solutions
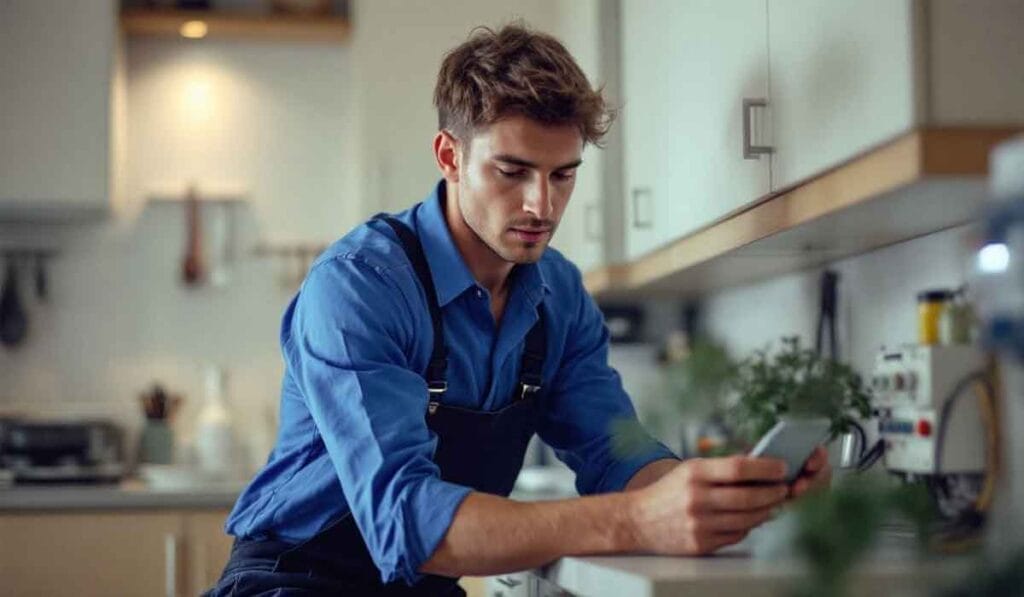
Surge protection is essential for electrical projects. It safeguards systems and prevents costly damages.
- Install surge protectors on power distribution systems to block sudden voltage spikes. Use options with high joule ratings for better durability.
- In your setup, choose surge devices compatible with extension cords and power cords. This ensures smooth operation and added safety.
- Use specialized protectors for sensitive electronics, such as programmable logic controllers (PLC) and embedded systems. These guard against damage during surges.
- Select units designed for emergency lighting and exit signs to maintain functionality during outages or power fluctuations.
- Opt for solutions with energy-efficient features that reduce waste while ensuring maximum protection across components like timers and filters.
Emergency disconnects and safety features
Emergency disconnects play a key role in protecting workers and equipment. These features ensure quick power shutdown during emergencies.
- Install emergency disconnects near main power sources for easy access. This is critical for urgent electrical projects.
- Choose disconnect switches with weatherproof enclosures for outdoor use. These ensure durability in varying conditions, including aerospace or automotive industry settings.
- Lockable disconnects should prevent accidental re-activation while maintaining electrical supplies or systems like air conditioning.
- Inspect the rating of your disconnects to ensure they match the load capacity of your wiring systems or power tools, such as bandsaws.
- Ensure compliance with safety standards to meet industry regulations, especially in high-risk locations using items like light-emitting diode (LED) systems.
- Replace worn grommets on emergency switches regularly to prevent short circuits or system failures.
Safety begins here but extends into control components, crucial for smooth operations in industrial settings.
Control Components
Control components keep your systems running smoothly. Use switches and relays to manage power flow efficiently.
Industrial switches and relays

- Industrial switches manage the flow of electricity in circuits. Toggle switches are ideal for simple on/off controls in machines. They are reliable, sturdy, and easy to use.
- Relays help automate systems by switching circuits using low-power signals. This makes them perfect for tasks requiring remote operation or high-speed switching.
- Heavy-duty switches can handle extreme conditions, such as high temperatures or vibrations, and are great for industries such as automotive or aerospace.
- Energy-efficient models reduce power consumption, saving operational costs over time. This is important in large-scale electrical projects.
- Proper installation ensures long-term performance and safety. Crimping tools and screws provide secure connections for these devices.
Understanding wiring options is key to pairing switches and relays effectively with systems you install next!
Control panel components
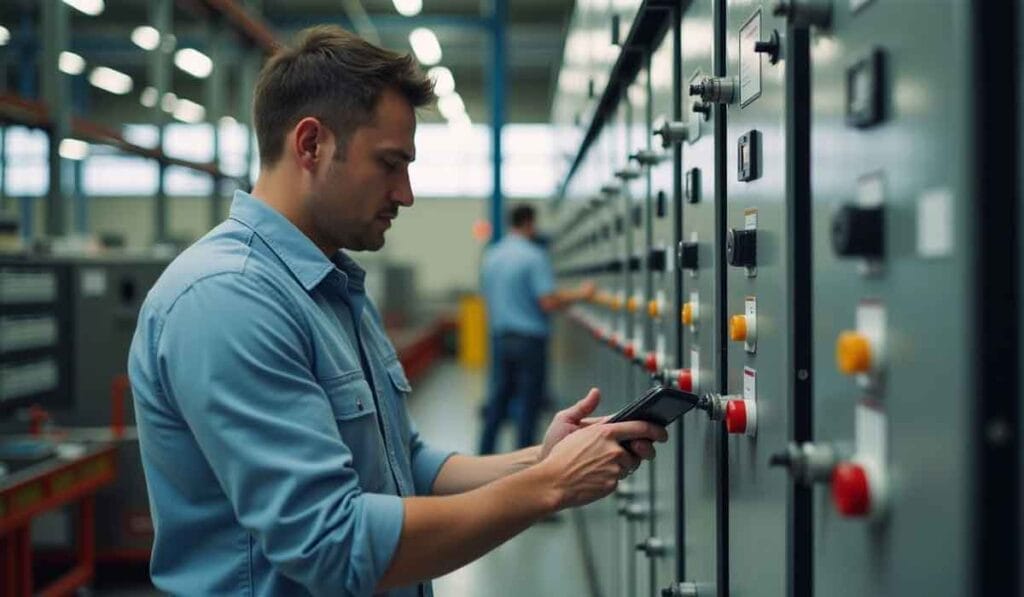
Control panel components play a key role in managing and automating electrical projects.
These parts help contractors like you enhance efficiency and safety on-site.
- Select durable enclosures to protect wiring from dust, moisture, and damage. For added durability, choose materials like stainless steel or TPR.
- Use high-quality contactors to control large power loads with ease. They ensure smooth operation for heavy-duty equipment in industries like aerospace or automotive.
- Install reliable terminal blocks for proper wiring connections. They simplify setups and reduce downtime during maintenance tasks.
- Include energy-efficient LEDs for clear status indications on panels. These lights use less power and are long-lasting, helping cut costs over time.
- Add programmable logic controllers (PLCs) to improve automation in complex systems. They optimize performance in applications requiring precision, such as PCB design or wire harness assembly.
- Choose efficient circuit protection devices to prevent overloads or short circuits inside the panel. This boosts safety during operation and protects your investment.
- Equip panels with resettable breakers to ensure quick recovery after faults occur without replacing fuses every time.
- Ensure user-friendly interfaces like switches or push buttons for easy manual control of systems when needed.
- Use advanced relays to handle signal switching with minimal wear over time.
Automation interface devices
Automation interface devices make machines smarter and easier to use. These tools connect systems, boost efficiency, and reduce errors in your electrical projects.
- Use Human-Machine Interfaces (HMIs) for clear control. They provide simple displays for data monitoring and adjustments.
- Install Programmable Logic Controllers (PLCs) to automate operations. They manage processes with fast, accurate responses.
- Choose input/output modules to link hardware with controllers. They transfer signals between devices effectively.
- Use industrial communication protocols like Ethernet/IP or MODBUS. These ensure smooth system communication in complex setups.
- Incorporate sensors and actuators for real-time feedback. They optimize performance across manufacturing systems.
- Add operator panels for better manual control options. These simplify troubleshooting during emergency electrical services.
- Pick scalable devices that grow with your needs over time. This saves on costs without sacrificing quality or safety features.
- Ensure the devices are compatible with your existing systems. This avoids downtime in automotive or aerospace industry applications.
- Focus on energy-efficient components to reduce power waste and save money in the long term.
- Trust vendor-managed inventory solutions to keep parts stocked for Just-in-Time (JIT) delivery schedules.
Wiring and Connectivity
Proper wiring and strong connections ensure smooth operations in your projects. Read more to pick the best solutions for your needs.
Cable types and applications
Different cables serve specific needs in electrical projects. You must choose the right type to ensure safety and efficiency.
- Shielded Cables: Use these to prevent interference in industrial electrical supplies or aerospace industry applications. They are ideal for sensitive systems.
- Unshielded Cables: These work well for less critical environments like standard power distribution systems. They cost less but lack protection against signals.
- Coaxial Cables: These are used in communication setups, such as connecting security cameras or data networks in automotive industry facilities.
- Fiber Optic Cables: These are ideal for high-speed data transfer, especially in automation or energy-efficient systems that require fast communication speeds.
- Power Cables: Install these for power distribution tasks, such as connecting transformers or circuit breakers to larger grids within industrial areas.
- Welding Cables are perfect for connecting heat exchangers or band sawing equipment where durability against heat and movement is essential on-site.
- Armored Cables: These are ideal for underground wiring needs or emergency electrical services, offering extra protection against physical damage and moisture.
Termination methods
Proper termination methods ensure reliable electrical connections. They improve safety and prevent faults in your electrical projects.
- Use crimp connectors for quick, secure terminations. Crimping reduces resistance and ensures a lasting connection.
- Apply soldering for precise and durable bonds. This works well for passive electronic components like diodes or light-emitting diodes (LEDs).
- Choose compression lugs for heavy-duty cables in industrial applications. They provide strong connections for power resistors and large wiring systems.
- Select push-in terminals to save time during installation. These are common in control panel assembly and automation devices.
- Strip wires accurately using a wire stripper tool. Avoid over-stripping to protect the conductor’s integrity in electronic components like taillights or plugs.
- Label every terminated wire properly to simplify troubleshooting later on. Clear labels help with vendor-managed inventory systems.
- Test all connections after termination for continuity and safety compliance, following industry regulations.
Installation best practices
Installing electrical components properly ensures safety and efficiency. Follow these best practices to achieve reliable results in your electrical projects.
- Double-check all measurements before starting. Precise measurements reduce errors during installation.
- Use the right cable type for your project. Match cables to voltage and current requirements.
- Ensure all connections are secure. Loose connections can cause overheating or failures.
- Follow industry safety standards while working. This includes wearing hard hats and using insulated tools.
- Label wires clearly during installation. Proper labeling prevents confusion during maintenance or repairs.
- Maintain a clean workspace at all times. Dirt or debris can damage sensitive electrical supplies.
- Use JIT delivery for essential components to avoid delays and ensure fresh stock availability.
- Inspect each component for defects before installing it. Faulty parts increase risks of failure or fire hazards.
- Securely mount control panels to prevent vibrations from loosening connections over time.
- Test all systems after complete setup to confirm they work as intended under load conditions.
Attention to wiring details ensures safe, durable systems that meet compliance standards outlined next in the guide!
Maintenance and Troubleshooting
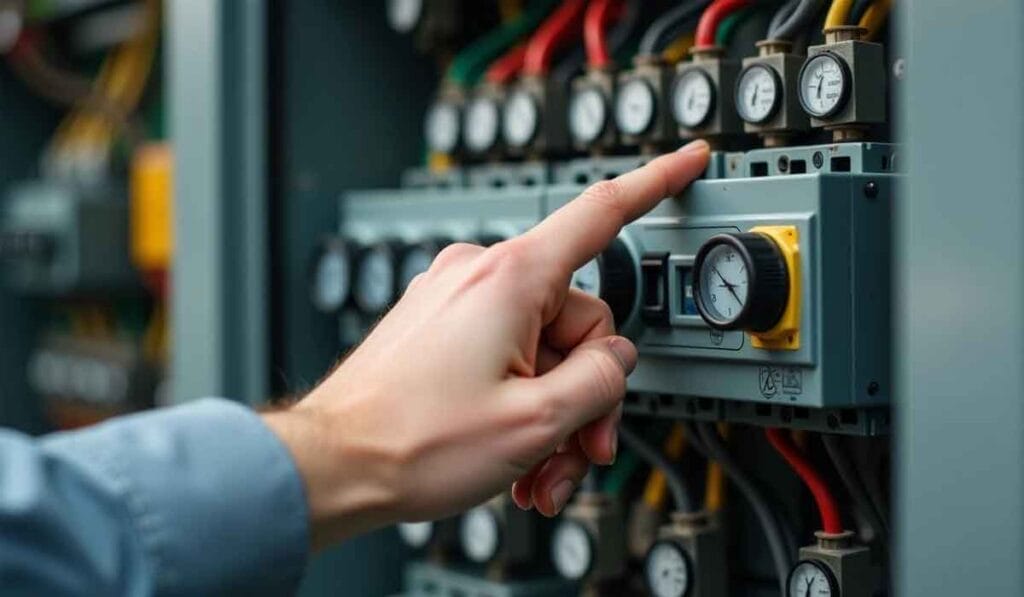
Regular care keeps electrical systems working well.
Quick fixes prevent bigger failures and costly downtime.
Common component issues
Electrical components are vital for your projects. Issues can slow you down or cause safety risks.
- Loose connections lead to overheating and arcing in cables or terminations. Check all connections regularly during electrical projects.
- Faulty circuit breakers may trip too often or fail to reset. Use high-quality electrical supplies from trusted sources like Babsco Supply.
- Overloaded transformers cause power loss and heat buildup. Ensure proper transformer selection based on specifications for industrial applications.
- Worn-out relays cause control issues in automation systems. To avoid delays in electrical projects, replace them when performance drops.
- Damaged wiring creates short circuits, increasing fire risks. Use durable cable types designed for specific uses in the aerospace industry or automotive industry.
- Corroded terminals reduce conductivity over time, leading to power failures. Apply proper termination methods with corrosion-resistant materials like titanium.
- Lack of surge protection leaves systems at risk of damage during voltage spikes caused by lightning or grid issues.
Move on to preventive maintenance tips that help avoid these problems before they start!
Preventive maintenance tips
Preventive maintenance keeps your projects running smoothly. It also ensures safety and saves money in the long term.
- Check components regularly for wear or damage. Look for cracks, corrosion, or discoloration on electrical supplies.
- Clean contact points to remove dirt or buildup. This improves performance and prevents overheating.
- Test circuit breakers annually to confirm proper function. Replace outdated models with energy-efficient options if needed.
- Inspect cables for cuts, frays, or exposed wires. Use high-quality cable types for long-lasting connections in industrial projects.
- Tighten loose connections in wiring systems often. Loose ends lead to power losses and safety risks over time.
- Use thermal imaging tools to find hotspots in electrical panels and components early. Fix issues before they grow into costly repairs.
- Schedule downtime for regular equipment maintenance checks during slower periods of work.
- Ensure control panel components like switches and relays perform correctly under load conditions.
- Replace outdated surge protection devices every few years as their effectiveness weakens.
Take proactive steps now to avoid bigger problems later while ensuring compliance with the standards that will be covered next!
When to replace vs. repair
Knowing whether to replace or repair electrical supplies can save time and money.
When deciding on electrical projects, focus on safety, reliability, and downtime.
- Check if the component causes frequent system failures. If repairs have not solved recurring issues, replace them.
- Inspect for physical damage, such as cracks or burns. Damaged parts often need replacement to ensure safety and compliance with industry standards.
- Assess the energy efficiency of old equipment. Upgrade outdated parts with modern, energy-efficient options like LED systems.
- Review the cost of repairs versus buying new components. If repair costs exceed half the price of a new part, replacing usually makes more sense.
- Test devices that are slow or unresponsive despite maintenance efforts. Swap them out for newer models to improve performance on industrial projects.
- Evaluate compliance with updated safety codes and certifications such as UL Standards or OSHA guidelines. Replace non-compliant equipment immediately.
- Determine aging signs in components nearing their service life expectancy (e.g., transformers lasting 20-30 years). Updating these ensures long-term system reliability.
- Look for irreparable wear in wiring connections, switches, or relays over time due to heavy usage by floor contractors or automotive industry tasks.
- Consider JIT delivery from a custom manufacturer if you urgently need replacements during emergency electrical services to minimize delays.
- Factor delays caused by sourcing hard-to-find spare parts for repairs into your decision-making process; opt for replacements from an extensive inventory instead of waiting weeks to fix it!
Compliance and Standards

Compliance with safety standards ensures proper working conditions for your projects.
Following industry regulations helps protect workers and equipment from risks.
Industry regulations
Follow strict industry regulations to ensure safety in all electrical projects.
The National Electrical Code (NEC) outlines mandatory standards for installations and materials.
Adhering to these rules prevents hazards and ensures reliable systems.
Use components with proper quality certifications like UL-rated products.
These meet high safety requirements for contractors working in aerospace or additive manufacturing.
Always check that your supplier aligns with Indiana-specific codes before beginning any project.
Quality certifications
Quality certifications ensure reliability and safety in electrical supplies.
To guarantee high performance, look for products that meet UL, ISO 9001, or CE standards.
These certifications confirm that components meet strict industry regulations and testing requirements.
Certified parts reduce risks on your electrical projects.
They provide consistency whether working in the aerospace industry or the automotive industry.
Using certified components also helps you comply with local and national safety standards while maintaining competitive prices on your materials.
Safety standards
Safety standards protect workers and equipment during electrical projects.
Reliable components reduce risks like shocks, fires, or system failures.
Follow industry regulations to ensure your worksite stays safe and efficient.
Use certified electrical supplies for all installations to meet compliance requirements.
Inspect safety features on emergency disconnects and surge protection devices before use.
Components should handle harsh conditions commonly found in the automotive or aerospace industries.
Proper adherence ensures safer flooring setups and energy-efficient systems and prevents costly accidents.
Move forward with power distribution solutions that match these high standards.
Conclusion
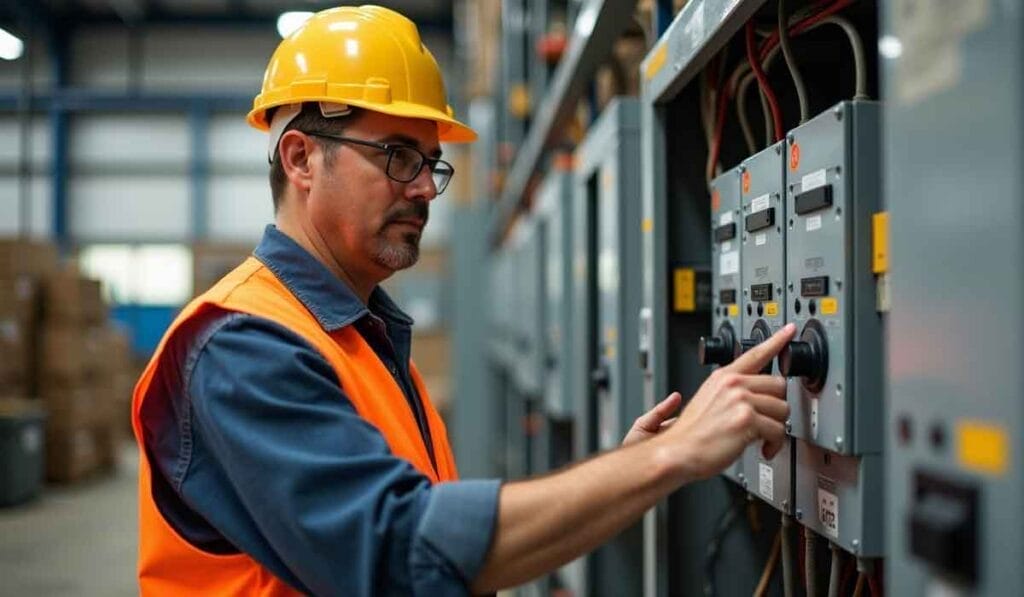
Choosing high-quality electrical components ensures safety, durability, and better performance for your projects.
Importance of choosing quality components
Using quality electrical supplies ensures safer and more reliable electrical projects.
High-grade components reduce risks like equipment failure, short circuits, or safety hazards.
They also meet strict industry regulations needed to protect workers and systems.
Using durable parts can handle demanding environments for contractors in fields like the aerospace or automotive industry.
Investing in trusted brands from suppliers like Babsco Supply helps assure better performance for your jobs.
Reliable components extend the system lifespan and minimize costly emergency electrical services later.
Long-term cost benefits
Choosing high-quality electrical supplies saves money in the long run.
Durable components last longer and require fewer repairs, reducing maintenance costs.
Reliable parts prevent unexpected breakdowns, keeping your electrical projects on track.
Energy-efficient products like LED systems cut energy bills over time. Industrial-grade items handle tough conditions better, lowering replacement needs.
Investing upfront leads to bigger savings for contractors working with tight budgets or demanding industries like aerospace or automotive.
Reliability factors
Reliability of electrical supplies is crucial for long-term cost savings.
High-quality components reduce downtime and prevent unexpected failures in electrical projects.
Reliable parts ensure consistent performance in tough industrial conditions, like those in the aerospace and automotive industries.
Use tested products with safety certifications to meet compliance standards while delivering dependable results.
Reliable systems also support energy-efficient designs, which lower operational costs over time.
FAQs
1. What types of electrical supplies are available for Indiana contractors?
We offer an extensive inventory of industrial-grade electrical components, including energy-efficient light-emitting diode (LED) products and materials for various electrical projects.
2. Can you provide custom manufacturing services for specific industries?
Yes, we work as a custom manufacturer to support the aerospace and automotive industries with tailored solutions, such as reverse engineering and specialized components.
3. Do you offer emergency electrical services for contractors in Indiana?
Yes, we provide emergency electrical services to ensure your projects stay on track without delays or disruptions.
4. How does Babsco Supply ensure fast delivery of electrical supplies?
We use JIT (Just-In-Time) delivery methods to get your needed items quickly while maintaining competitive prices.
5. Are bucket truck services included in your offerings for large-scale projects?
Yes, bucket truck support is available to help contractors handle complex or high-elevation tasks efficiently during their projects.